PEER Construction, through the commitment and involvement of management and workers, is dedicated to the safety of all employees. contractors, apprentices, and subcontractors.
PEER Construction seeks to ensure the use of safe work practices during all tasks involved in our operations, consistent with the organisation’s duty of care under Work Health and Safety legislation.
Purpose
The purpose of this policy is to:
- set a standard for PEER Construction in terms of WHS risks and PPE requirements.
- align with the standard set by the PEER Construction Policy and procedures manual and legislative requirements, especially Work Health and Safety Act 2012 (SA) and the Environment Protection Act 1993.
Scope
This policy aims to protect the employees of PEER Construction from exposure to workplace hazards and the
risk of injury through the use of personal protective equipment (PPE).
Using PPE
The need to use PPE shall be determined from the process of hazard identification, risk assessment and development of risk control measures.
PPE is not a substitute for more effective control methods and its use will be considered only when other means of protection against hazards are not adequate or feasible. It will be used in conjunction with other controls unless no other means of hazard control exist.
PEER Construction will provide PPE to employees. Apprentices, contractors and subcontractors are responsible for providing their own.
All PPE must be maintained in good, functional order and compliant with Australian Standards where applicable.
Examples of PPE
Specific PPE may be required to be worn under certain circumstances. This may include:
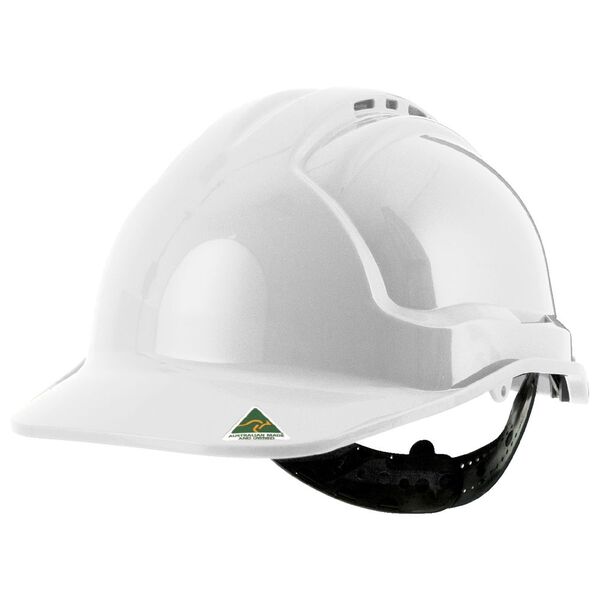
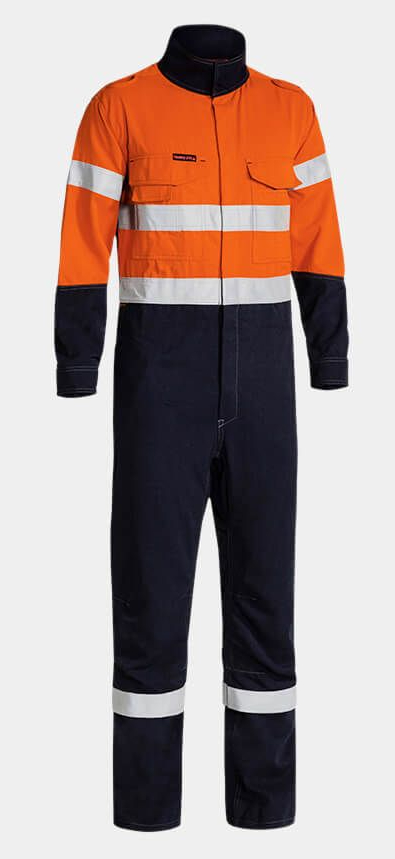
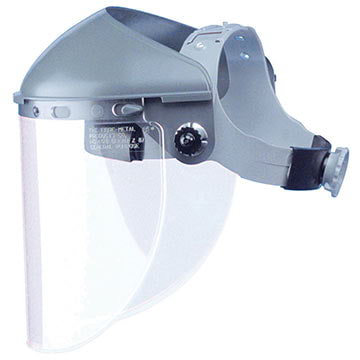
Head protection
A safety helmet shall be worn where there is a possibility that a person:
- may be struck on the head by a falling object
- the person may strike their head against a fixed object
- is likely to have inadvertent head contact with an electrical hazard.
Full body protection
Where there is risk of dermal exposure to specific infection agents or hazardous chemicals.
Eye protection / face shield
Where a risk of eye injury exists. Typical hazards might include flying particles, dust, splashing substances, harmful gases, vapours, aerosols, and high intensity radiation.
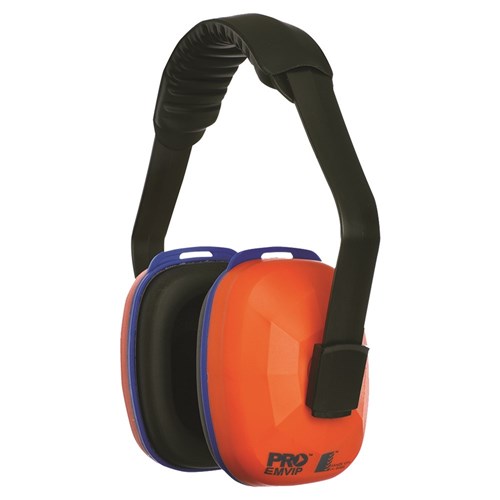
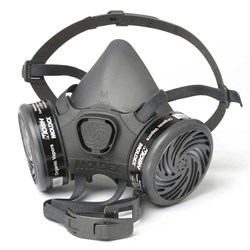
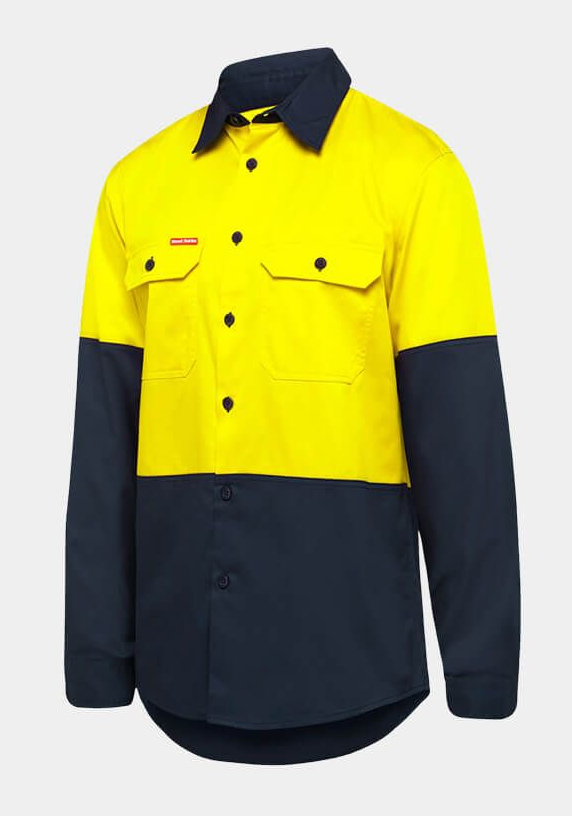
Hearing protection
Where a risk of noise induced hearing loss exists. The need for hearing protection shall be assessed from the conduct of noise monitoring surveys in potential noise hazard areas.
Respiratory protection
Where all other practicable measures have been taken to provide control measures to ensure that no employee is exposed to an atmosphere that is or may be injurious to health.
Protective clothing and sunscreen
Where employees work outdoors are exposed to the sun for continuous periods direct exposure to UV radiation shall be minimised by providing hats, long sleeves/trousers and an adequate supply of sunscreen.
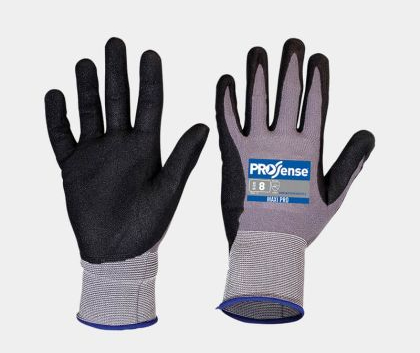
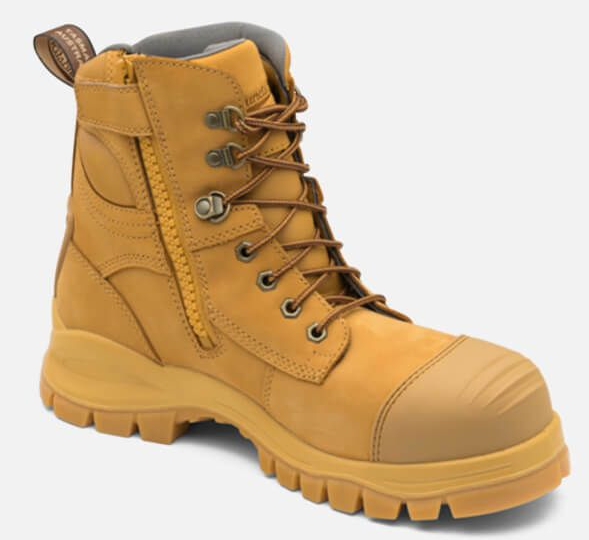
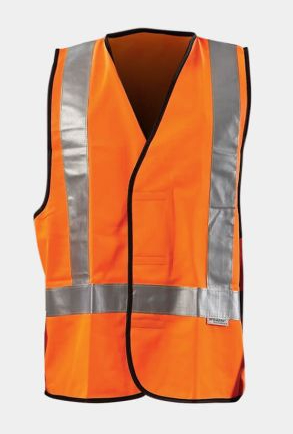
Hand protection
Where there is an identified hazard with a potential for hand injury, transmission of infection or absorption of substances via the skin.
Protective footwear (safety footwear)
Shall be provided where the work exposes the employee to a medium to high risk of injury to feet.
High visibility retro reflective safety vests
Where there is a risk of injury associated with working on or near roadways, near moving traffic or plant or other circumstances where high visibility of the worker is required.
Cleaning and maintenance
It is important that all PPE be kept clean and properly maintained. Cleaning is particularly important for eye and face protection where dirty or fogged lenses could impair vision. Employees must inspect, clean, and maintain their PPE according to the manufacturers’ instructions before and after each use. Supervisors are responsible for ensuring that users properly maintain their PPE in good condition.
Personal protective equipment must not be shared between employees until it has been properly cleaned and sanitized. PPE will be distributed for individual use whenever possible.
If employees provide their own PPE, make sure that it is adequate for the workplace hazards, and that it is maintained in a clean and reliable condition.
Defective or damaged PPE will not be used and will be immediately discarded.
It is also important to ensure that contaminated PPE which cannot be decontaminated is disposed of in a manner that protects employees from exposure to hazards.
Supervisor responsibilities
- Implementing and enforcing PPE use and policies in their work area.
- Providing appropriate PPE and making it available to employees.
- Ensuring that employees are trained on the proper use, care, and cleaning of PPE.
- Ensuring that PPE training certification and evaluation forms are signed and given to PEER Construction.
- Ensuring that employees use and maintain their PPE correctly.
- Notifying PEER Construction site supervisor and safety officer when new hazards are introduced or when processes are added or changed.
- Ensuring that defective or damaged PPE is immediately disposed of and replaced.
Employee responsibilities
- Wearing PPE as required.
- Attending training sessions if required.
- Properly caring for, cleaning, maintaining, and inspecting PPE as required.
- Informing the supervisor when PPE needs to be repaired or replaced.
Work Health and Safety Act 2012 (SA)
Work Health and Safety Regulations 2012 (SA)
Environment Protection Act 1993
Relevant Australian Standards
WHS Policy
Version 1.0 – Last updated 6/2/2022